
Wycinarki laserowe Kimla z napędami liniowymi, umożliwiają szybkie i wydajne wycinanie dowolnych kształtów z arkuszy blach. Wyjątkowo wysokie prędkości i przyspieszenia bez ograniczania zrywu w połączeniu z układami pomiarowymi o wysokiej rozdzielczości umożliwiają osiągnięcie niespotykanej wydajności i dokładności cięcia.
W laserach Fiber Linear firmy Kimla uzyskano niespotykaną do tej pory na świecię dynamikę, dzięki zastosowaniu ultranowoczesnych absolutnych układów pomiarowych położenia o rozdzielczości 1 nm firmy Renishaw, regulatorów pozycji, prędkości i przyspieszenia oraz systemu sterowania z Dynamiczną Analizą Wektorów.
Różnica w pracy Laserów Fiber Linear firmy Kimla w stosunku do laserów CO2 jest szczególnie zauważalna w przypadku blach cienkich do 8mm. Koszt wycięcia detalu Laserem Kimla Linear można obniżyć wielokrotnie. Umożliwia to znacznie większa sprawność energetyczna, dochodząca do 35% (w laserach CO2, tylko do 5%) oraz większa koncentracja energii, wynikająca z krótszej długości fali światła.
Lasery światłowodowe Firmy Kimla posiadają liczne atuty: doskonałą jakość i wysoką wydajność przy możliwości ich dostosowania do indywidualnych potrzeb klienta. Dodatkową zaletą laserów firmy Kimla jest ich korzystna cena.
Lasery Kimla produkowane są w zależności od potrzeb, w różnych konfiguracjach i obszarach roboczych. Różnorodność ta dotyczy: stopnia automatyzacji, mocy źródła lasera oraz wyposażenia. Firma Kimla produkuje lasery zarówno z jednym stołem roboczym, których istotnym czynnikiem jest wysoka wydajność przy niskiej cenie jak i lasery produkcyjne z automatyczną wymianą palet, z systemami odciągowymi, oraz oprogramowaniem do nestingu i przygotowania produkcji.
Lasery produkcyjne są maszynami o większej wydajności, prędkości maksymalnej i przyspieszeniach. Lasery światłowodowe Kimla dzięki unikalnym możliwościom bardzo szybkiego cięcia cienkich blach doskonale nadają się do wycinania jako alternatywa dlaa wykrawarek rewolwerowych, które dotychczas były uznawane za najtańszą technologię cięcia elementów z blach.
Atutem laserów światłowodowych KIMLA jest ich wysoka jakość i wydajność oraz możliwość ich dostosowania do indywidualnych potrzeb klienta przy korzystnej cenie, znacznie atrakcyjniejszej, niż w przypadku innych urządzeń oferowanych na rynku.
Firma Kimla jako pierwsza na świecie zintegrowała system drukowania do opisywania wycinanych detali. Już nie musisz ręcznie opisywać detali po ich wycięciu. Przed cięciem specjalna głowica drukująca naniesie opisy detali na arkusz blachy. Wszystkie detale po wycięciu będą już łatwo identyfikowane: zobacz film - drukowanie opisów na laserze fiber »
Dostępna jest również już opcja głowicy skanujęcej do lasera do skanowania istniejących detali co uwalnia nas z czasochłonnego przerysowywania istniejących fizycznie części i znacznie skraca czas przygotowania projektu.
Dla klientów posiadających lasery niemieckiej firmy wprowadziliśmy opcję importu plików *.GEO ułatwiając przejście na wydajne lasery firmy Kimla. Nie trzeba już konwertować tysięcy plików GEO zgromadzonych przez wiele lat.
Ważne artykuły
Model lasera | Finecut | Flashcut | Powercut | Extremecut |
---|---|---|---|---|
Moc lasera | do 2kW | do 4kW | do 8kW | do 12kW |
Obszar roboczy (mm) | 1000 x 2000 1500 x 3000 |
1000 x 2000 1500 x 3000 2000 x 4000 |
1000 x 2000 1500 x 3000 2000 x 4000 2000 x 6000 2000 x 8000 2000 x 10000 2500 x 3000 2500 x 6000 2500 x 8000 2500 x 12000 |
1000 x 2000 1500 x 3000 2000 x 4000 2000 x 6000 2000 x 8000 2000 x 10000 2500 x 3000 2500 x 6000 2500 x 8000 2500 x 12000 |
Zakres osi Z | 100 mm | 100 mm | 100 mm | 100 mm |
Napędy liniowe | tak | tak | tak (HP) | tak (HP) |
Automatyczny zmieniacz palet | nie | tak | tak | tak |
Laserowe bariery bezpieczeńśtwa | nie | tak | tak | tak |
Drzwi z każdej strony lasera | tak | tak | tak | tak |
Odpylacz z filtrami Ultraweb | nie | tak | tak | tak |
Zmienna ogniskowa głowicy (zoom) | nie | opcjonalnie | tak | tak |
Belka z kompozytów węglowych | nie | nie | nie | tak |
Sterowanie i oprogramowanie | ||||
System sterowania CAD/CAM/NEST/CNC | tak | tak | tak | tak |
Nesting z zarządzaniem produkcją | opcjonalnie | 1 stanowisko | 1 stanowisko | 2 stanowiska |
Połączenie z systemem ERP | nie | opcjonalnie | tak | tak |
Wycinanie w locie (flycut) | opcjonalnie | tak | tak | tak |













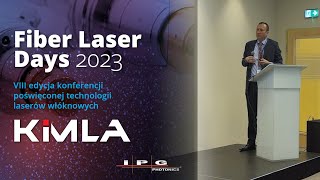

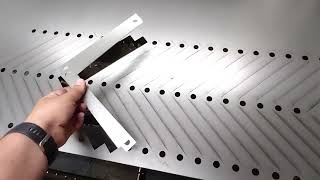

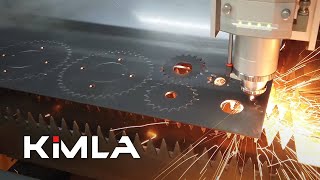

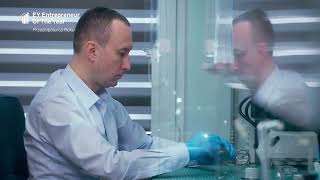

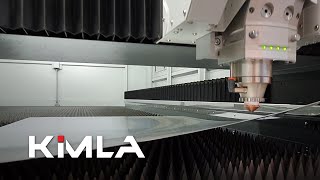

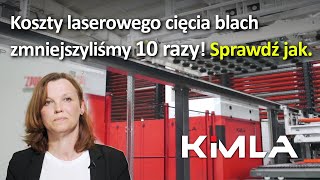

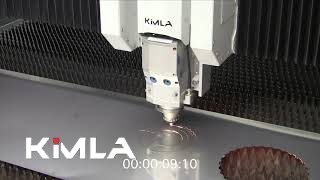



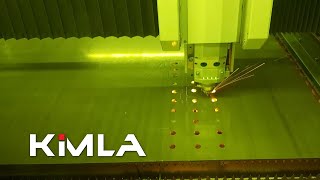

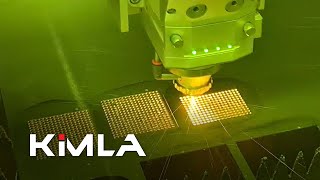

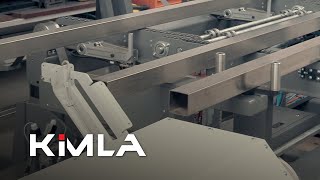

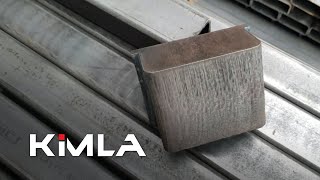

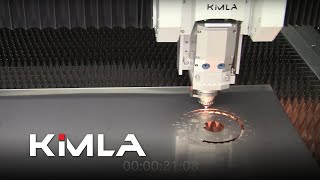



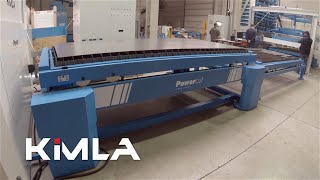



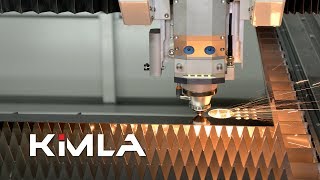

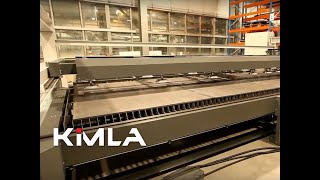

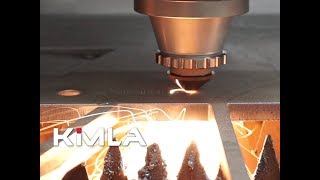

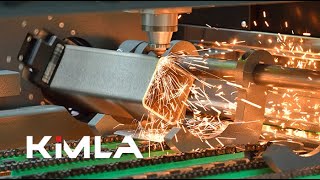

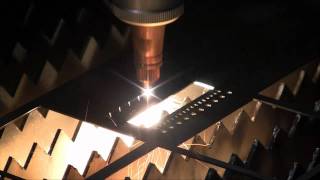

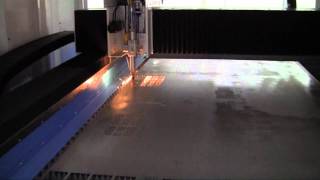

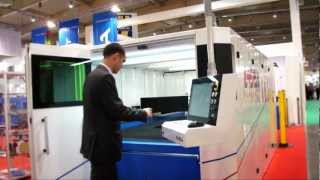

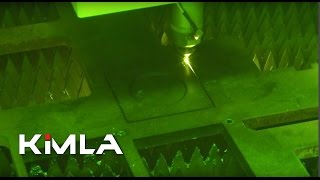

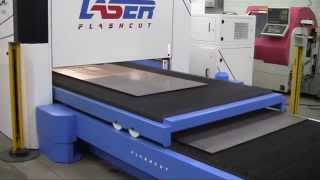

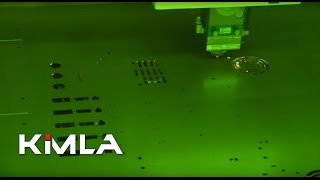

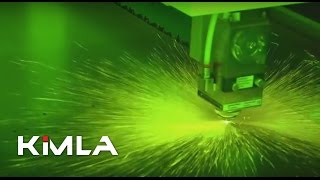

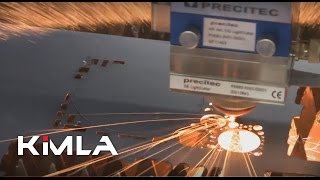

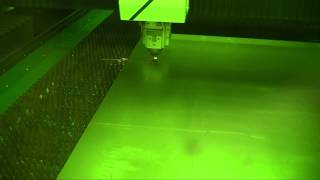

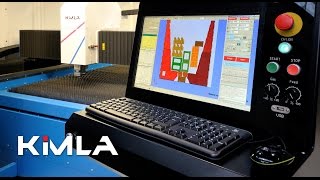

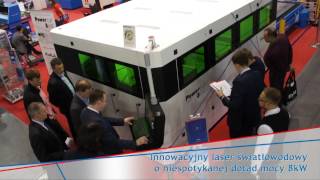

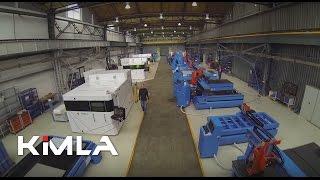

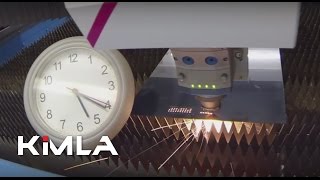

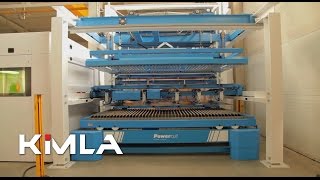

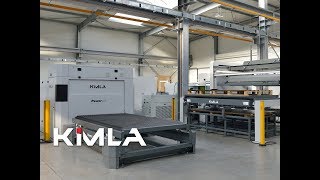

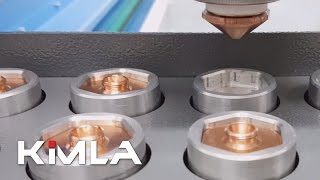
